How to Make a Paper Bag: From Raw Materials to Retail Brilliance
Discover how to make a paper bag and where paper bags come from. Learn about materials, history, manufacturing, and why custom paper bags matter for your brand.
Contact Us now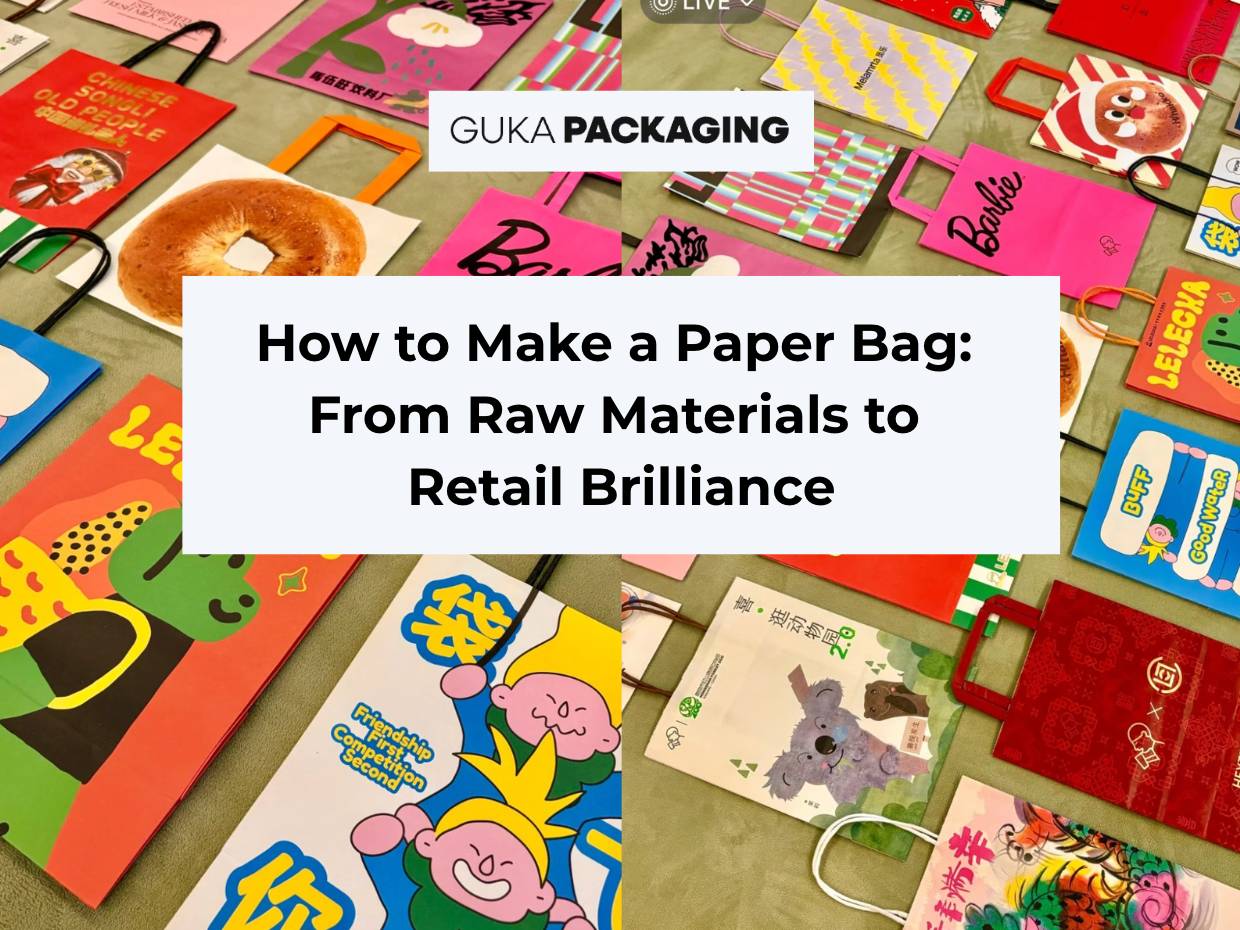
Table of content
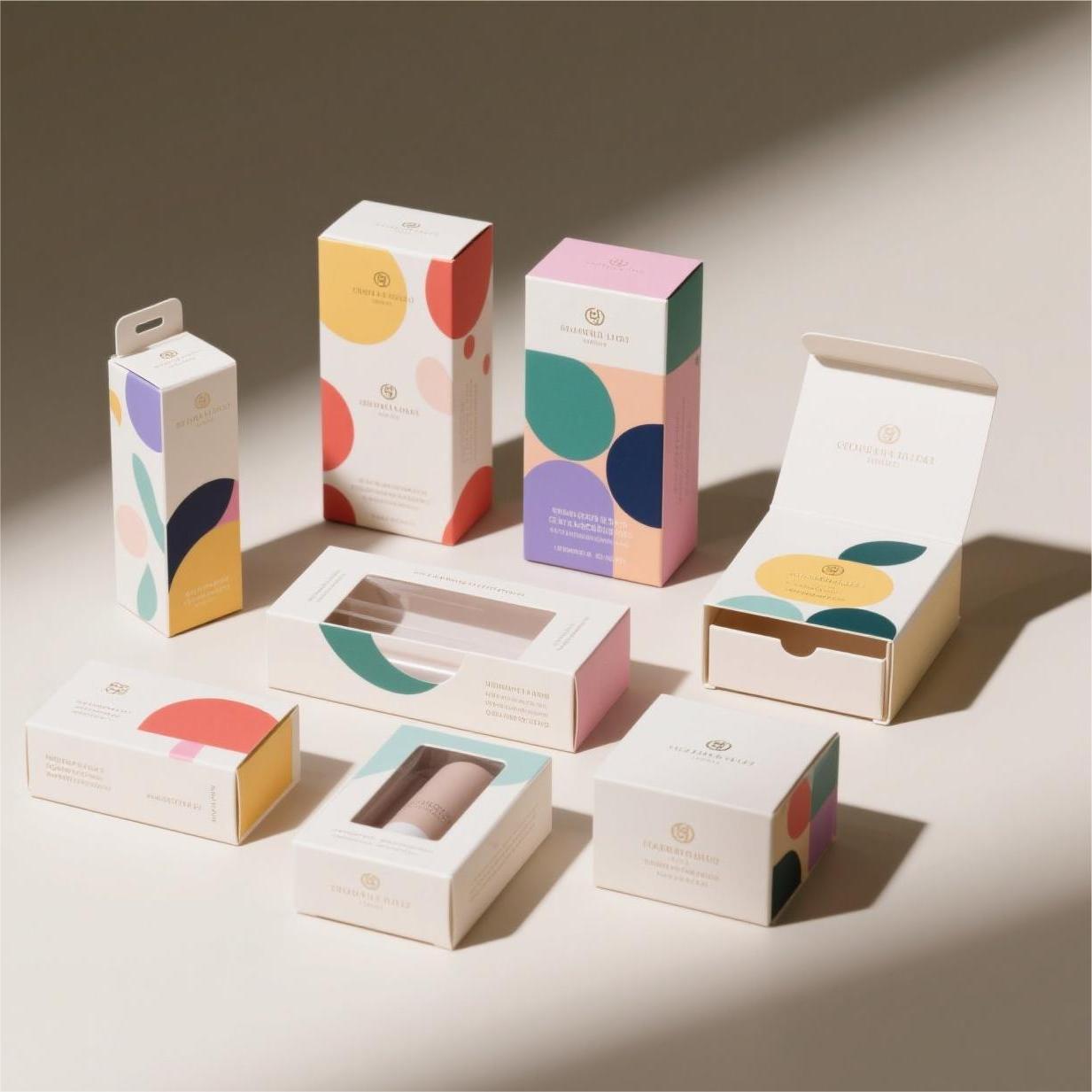
Ready to Elevate Your Brand with 100% Custom Box & Bag Solutions?
Get a Free QuoteWhy Paper Bags Matter More Than Ever
In today’s eco-conscious world, paper bags have become much more than just a vessel for carrying goods—they’re a symbol of sustainability, branding, and functionality. Whether it’s for luxury retail, gourmet food, cosmetics, or wine packaging, paper bags are widely embraced for their biodegradability, durability, and custom appeal. But have you ever wondered how to make a paper bag, or where paper bags come from?
In this article, we’ll take a close look at:
- How paper bags are made
- What materials they use
- The history behind their invention
- Why they’re better than plastic bags
- And why brands around the world are choosing custom paper bag solutions
Let’s unpack the full story.
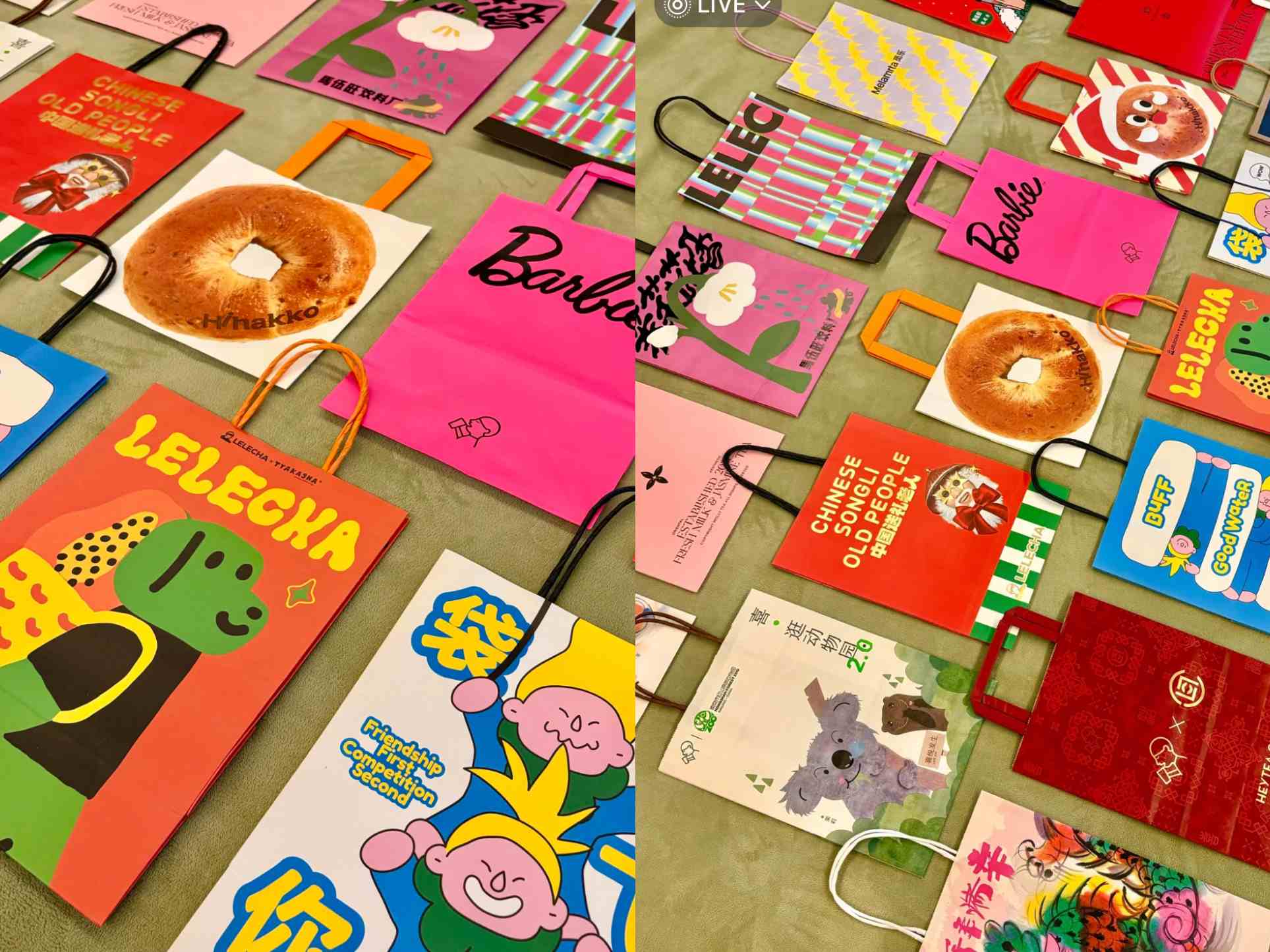
Where Do Paper Bags Come From? A Brief History
Who Invented Paper Bags?
The origins of the modern paper bag date back to 1852, when Francis Wolle, an American schoolteacher, patented the first machine to mass-produce envelope-style paper bags. Later, in 1871, Margaret E. Knight revolutionized the industry by inventing the flat-bottom paper bag, making it far more practical for everyday use.
By 1883, Charles Stilwell developed the “self-opening sack” (SOS) bag—an upright, stackable version that still influences designs today.
Fun fact: Plastic bags weren’t introduced until the 1960s, meaning paper had already dominated for decades. (Source: Smithsonian Magazine)
When Were Paper Bags Invented?
- 1852 – First paper bag machine
- 1871 – Flat-bottom bag design
- 1883 – SOS bag innovation
- 1912 – Handles added for easier carrying
How Are Paper Bags Made Today?
Step-by-Step Paper Bag Production Process
At modern paper bag factories, the process has become highly automated and efficient. Here’s how paper bags are made:
- Raw Material Selection
- Most bags use kraft paper, made from virgin or recycled wood pulp.
- For moisture resistance, some bags use laminated kraft paper.
- Paper Cutting: Paper rolls are cut to precise dimensions based on the bag’s intended size.
- Folding & Gluing: Machines fold the paper into the desired shape and apply adhesive to seal the sides and bottom.
- Printing:Branding elements like logos, colors, and slogans are added using offset or flexographic printing.
- Handle Attachment: Handles (twisted, flat, or rope) are glued on using automated systems.
- Final Inspection & Packaging: Bags are quality-checked, stacked, and packed for shipping.
This streamlined process ensures high-volume production while maintaining brand consistency and eco standards.
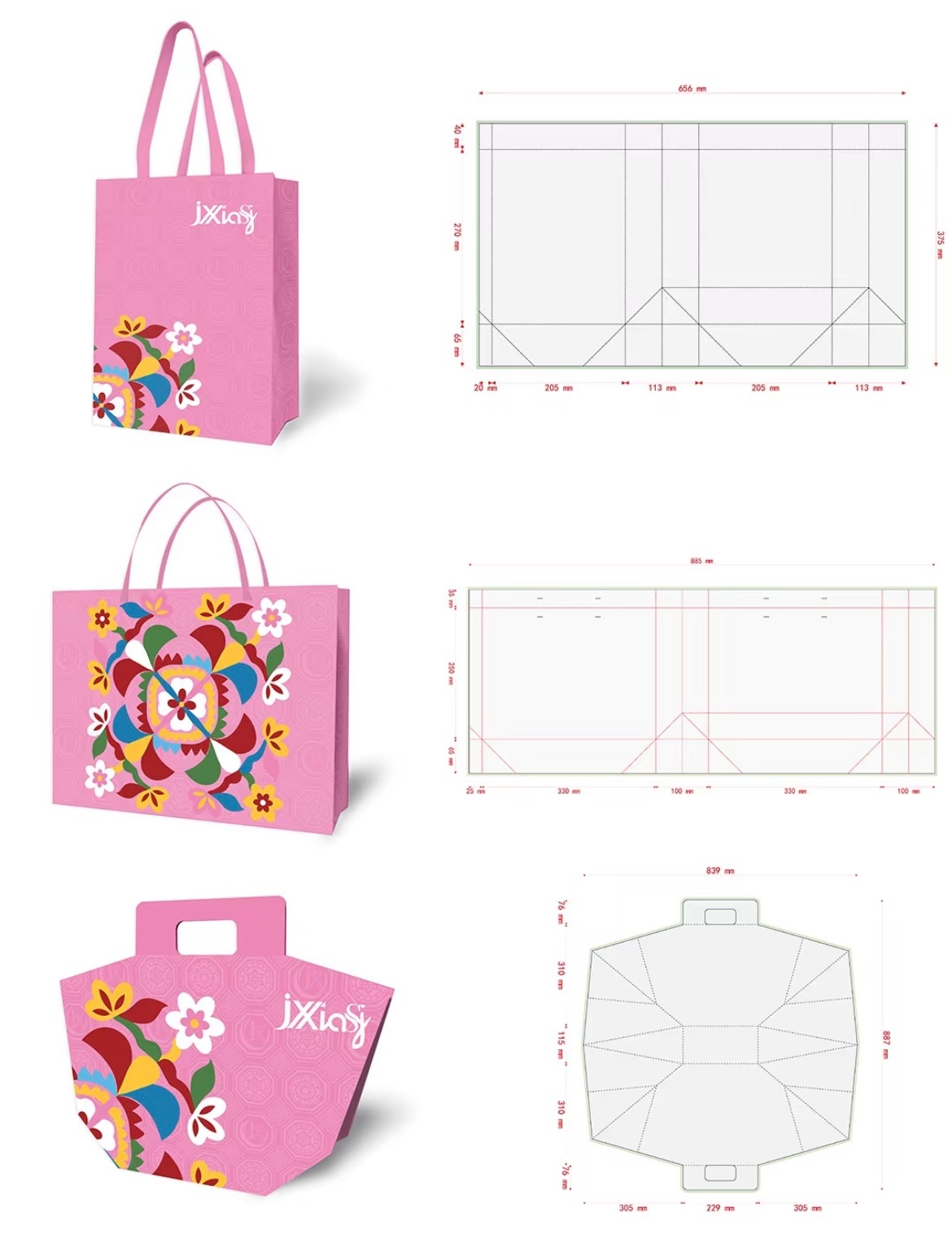
Related Blog: Printing on Cardboard Boxes: 8 Common Box Print Methods Explained
What Are Paper Bags Made Of?
Common Paper Bag Materials
At GUKA Packaging, we help you select the best paper bag material based on your product type, branding goals, and sustainability preferences.
Paper Bag Sizes by Number: Understanding the Format
In paper bag manufacturing, sizes are often denoted by number codes such as #6, #8, #12, #16, etc. Here’s a quick breakdown:
- #6: Small lunch bags
- #8: Standard grocery bag
- #12: Ideal for retail stores (clothing, accessories)
- #16: Larger bags for wine, gifts, or apparel
For custom dimensions tailored to your product, GUKA provides fully personalized sizing and printing services.
What Are the Functions of Paper Bags?
Paper bags serve a variety of functions across industries:
- Retail: Stylish branding & consumer convenience
- Ecommerce: Lightweight, sustainable shipping solution
- Food & Beverage: Breathable, grease-resistant variants
- Cosmetics & Luxury: Premium look with embossing or foil stamping
- Gifting: Custom handles, textures, and finishes for added impact
Are Paper Bags Biodegradable?
Yes—paper bags are fully biodegradable, especially when made from uncoated kraft or recycled paper. Unlike plastic, which takes centuries to decompose, a standard brown paper bag can break down in 2 to 6 weeks under composting conditions.
GUKA Packaging’s custom paper bags are:
- Compostable
- Recyclable
- Made from FSC-certified sources upon request
Learn more about our eco-friendly packaging solutions
Why Choose Custom Paper Bags Over Generic Options?
Benefits for Your Brand
- Memorable unboxing experience
- Increased brand recall on the street
- Supports sustainable brand image
- Adaptable for every industry: wine, apparel, skincare, food, toys, and more
Trusted Paper Bag Manufacturer: GUKA Packaging
With over 500 global clients across the U.S., Europe, Australia,etc., GUKA delivers fully customized paper bag solutions with:
- Low MOQs (starting from 500-2000 pcs)
- Custom sizes, colors, and finishes
- Premium printing (foil, emboss, spot UV)
- Rigid QC and fast lead times
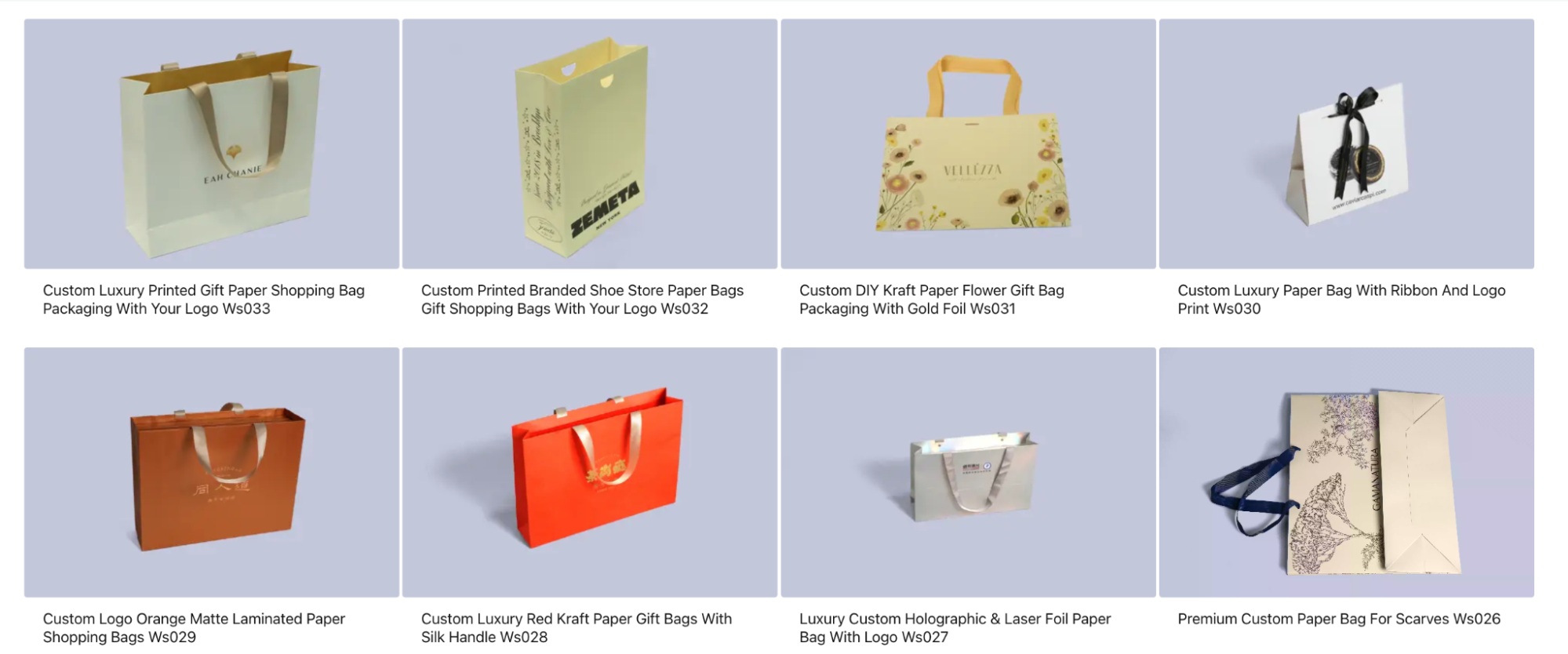
Conclusion: Craft Your Brand's Future with Custom Paper Bags
From its 19th-century origins to its 21st-century sustainability mission, the paper bag continues to evolve. Whether you’re wondering how to make a paper bag, what it’s made of, or why it's better than plastic, one thing is clear—paper bags are essential for eco-friendly, brand-forward businesses.
At GUKA Packaging, we help you turn a simple paper bag into a powerful storytelling tool. Whether you need stylish gift bags, luxury retail packaging, or food-safe takeaway solutions, we’re here to make it happen.
Get a quote today and explore how we can elevate your packaging with custom paper bag manufacturing.
Recommended for you
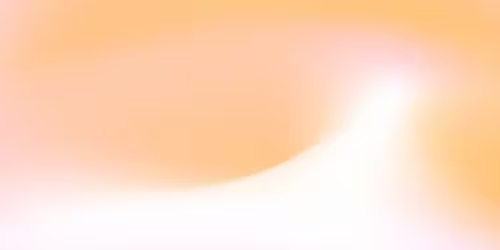